How to create, build, and ship faster - for manufacturing businesses, there is a better way than spreadsheets and ERPs.
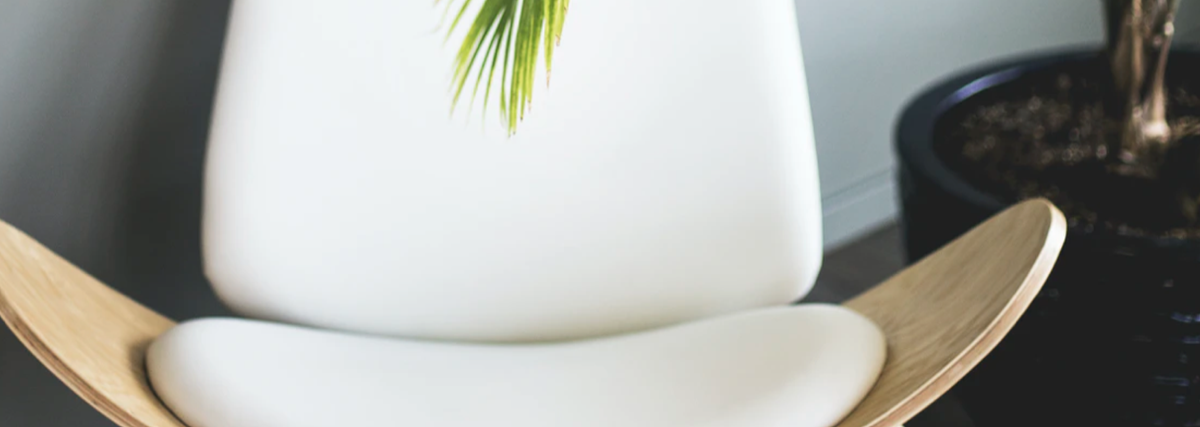
Who is this for?
For manufacturers, creators, and designers of products that need to be shipped: ditch manual processes and scale your operations with our templates for manufacturing businesses.
Problem
1) Lack of smooth, centralized process to manage everything from A-Z: Businesses that manufacture and ship products have three options: a) Use spreadsheets + additional tools/apps like appsheets, b) Use either old and clunky ERPs or new, but expensive and rigid ERP/ manufacturing management systems that force you to adapt your processes to their pre-set workflow, and c) Internally develop a highly customizable software for your operations.
Going with the first option means using multiple different tools - this leads to additional bottlenecks and frictions: slowing down your operations. The second option can be too expensive and cumbersome: forcing you to force fit your process into an already pre existing structure: this is not the best way to achieve smooth and fast operations. Final option is ideal in theory - but extremely time-consuming and costly in practice.
2) Lack of automations: Using multiple different tools for assembly line operations, inventory management and shipments, means lack of fast automations: there are too many tools and therefore, potential bottlenecks - ultimately reducing the speed and efficiency of your operations.
3) Lack of real-time data analytics: Unless you are using some expensive ERP solution, gaining a real-time data analytics overview is going to be exceptionally difficult - since one central application is not being used for everything, the process cannot be analyzed as a whole. This means that conducting operational autopsies and root cause analyses will be extremely difficult: accomplishing improvements to speed and efficiency would become extremely challenging.
Solution
And this is where Jestor comes in:
Use Jestor’s furniture manufacturing template to increase speed & efficiency of your operations: build, sell, and deliver more products in a shorter amount of time - ultimately, generating more revenue.
Overall
Jestor | Other Options |
A no-code relational database that ensures a complete & holistic process: accommodating everything from initial orders to final deliveries. | Have to adapt to your ERP of choice or use multiple tools to achieve a harmonious (yet still inefficient) solution to the complexity of the operations. |
Automations & trigger: to enable efficient communication and project management for team members. The process is smooth and complete. There are no breakages and manual processes in between. | Little (if any) automations: Import & export and juggle multiple tools, or use old and clunky ERPs or expensive Manufacture Management Systems. |
Data interlinked and connected in a meaningful way: all relevant and related records are connected effortlessly. You can scale faster and ensure access to better & more accurate analytics: empowering you with a complete picture of your entire manufacturing operations. Bottlenecks are easy to spot, and improvements can therefore be implemented with speed & scale: helping you to reduce waste & generate more revenue. | Have to use an inflexible hardcoded ERP, or rely on spreadsheets: where records are not truly connected to each other: accurate analytics and overview are impossible to accomplish. You cannot spot problems and inefficiencies quick enough to prevent waste and slowdowns to revenue growth. |
https://jestor.com/template/simple-furniture-manufacturing-beta/
https://jestor.com/template/simple-furniture-manufacturing-beta